Graphite electrodes play a crucial role in the operation of electric arc furnaces (EAFs), which are widely used in steelmaking and other metallurgical processes. Understanding how to effectively manage these electrodes is essential for optimizing furnace performance, reducing costs, and ensuring product quality. In this blog, we will explore best practices for handling graphite electrodes in arc furnaces, including their selection, installation, maintenance, and environmental considerations.
Understanding Graphite Electrodes
Graphite electrodes are made from high-quality petroleum coke and pitch, which are processed to create a material that can withstand the extreme temperatures generated in an electric arc furnace. These electrodes conduct electricity and create the arc that melts scrap metal and other raw materials.
Key Functions of Graphite Electrodes:
1. Electrical Conductivity: They provide the necessary electrical conductivity to generate heat.
2. Heat Generation: The arc produced between the electrodes generates the high temperatures required for melting metals.
3. Chemical Stability: Graphite electrodes are chemically stable at high temperatures, making them suitable for various metallurgical processes.
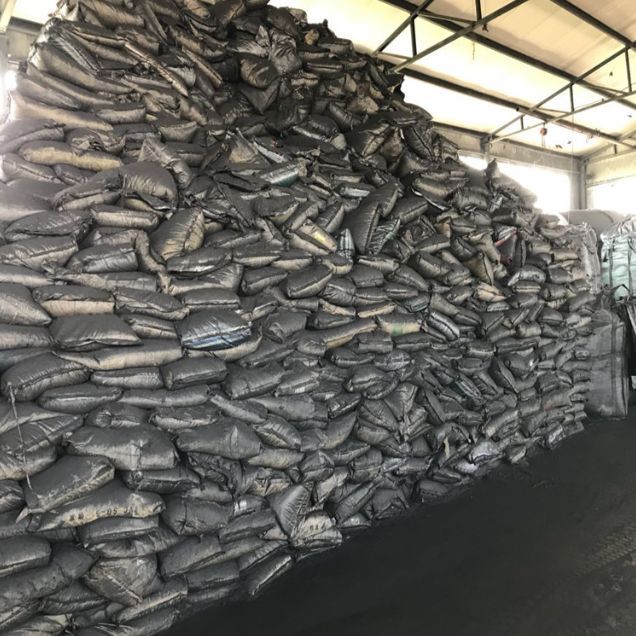
Best Practices for Handling Graphite Electrodes
1. Selection of Quality Electrodes
Choosing the right graphite electrodes is the first step in ensuring efficient furnace operation. Consider the following factors:
• Grade and Quality: Opt for high-quality electrodes with low resistivity and high thermal conductivity. This will enhance the efficiency of the melting process.
• Diameter and Length: Select electrodes that match the specifications of your furnace. The diameter affects current carrying capacity, while the length influences the arc stability.
2. Proper Storage
Graphite electrodes should be stored in a dry, clean environment to prevent contamination and damage. Here are some storage tips:
• Avoid Moisture: Store electrodes in a moisture-free area to prevent degradation.
• Protect from Physical Damage: Use racks or pallets to keep electrodes off the ground and prevent physical damage during handling.
3. Installation Techniques
Proper installation of graphite electrodes is crucial for optimal performance:
• Alignment: Ensure that electrodes are aligned correctly to maintain a stable arc and prevent uneven wear.
• Connection: Use appropriate connection methods (e.g., threaded or clamp connections) to ensure a secure and reliable electrical connection.
4. Monitoring and Maintenance
Regular monitoring and maintenance of graphite electrodes can significantly extend their lifespan:
• Wear Monitoring: Keep track of electrode wear and replace them as needed to avoid operational issues.
• Temperature Management: Monitor the temperature of the electrodes during operation to prevent overheating, which can lead to premature failure.
5. Environmental Considerations
Handling graphite electrodes also involves addressing environmental concerns:
• Dust Control: Implement measures to control dust generated during the handling and operation of electrodes. This can include using dust suppression systems and proper ventilation.
• Recycling: Explore recycling options for used electrodes. Many facilities can repurpose spent electrodes, reducing waste and promoting sustainability.
Conclusion
Effectively dealing with graphite electrodes in electric arc furnaces is essential for maximizing efficiency, reducing costs, and ensuring high-quality production. By selecting quality electrodes, implementing proper storage and installation techniques, monitoring wear, and addressing environmental considerations, you can enhance the performance of your arc furnace operations.
If you have any questions or need assistance with graphite electrodes for your electric arc furnace, feel free to reach out. Together, we can optimize your operations and achieve greater success in your metallurgical processes.
Post time: 9 月-09-2024